At the end of 2021 we shipped to our Swiss client SetzFensterbau AG a complete Woodpecker 60 production line – a compact solution for large production outputs that boasts several interesting technological solutions such as the intelligent stacking unit and a rack storage unit for the storage of finished pieces.
The line for the production of wooden doors and windows Woodpecker 60, delivered just shortly before Christmas to the Swiss company SetzFensterbau AG is now fully operational.
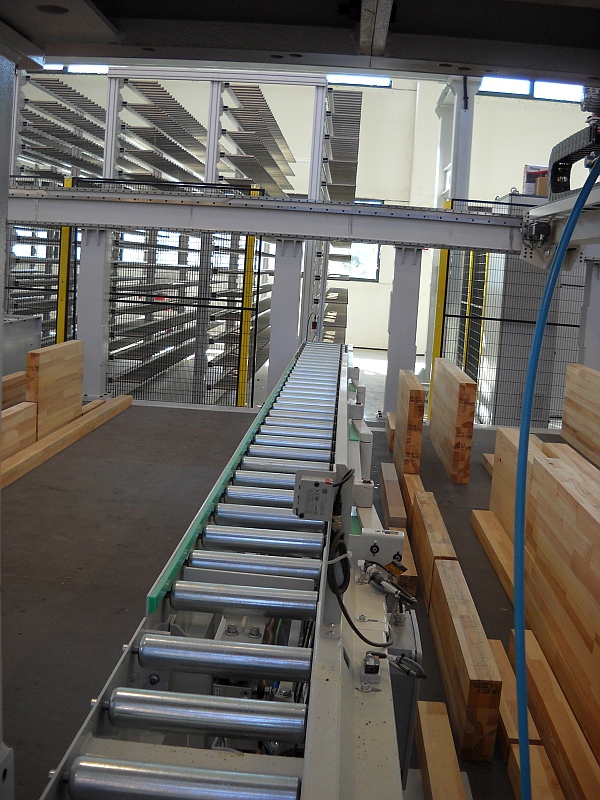
This project has been one of the most arduous challenges we have completed recently. The system, designed and mechanised especially for our client, consists of various components:
- EcoLine sanding machine;
- Everest intelligent stacking unit;
- Woodpecker 60 robotized machining cell;
- Ultrasound bath for tool washing;
- “Pro Flow” horizontal profile flow-coating machine;
- “Pro Dry” profile fast drying tunnel;
- Rack storage unit for finished pieces.
It all starts with the optimized transfer of the load that brings the pieces to the sanding machine and on to the Woodpecker 60 machining cell. The pieces then go through the flow-coating machine and are stocked in the rack storage unit.
Throughout the process, each piece is always identified at subsequent laser checks, via an initial QR Code or Barcode, for height, width and thickness. Finally, prior to final output, each piece is laser-marked..
The project began to take shape in 2020 when the Swiss client expressed their need to install in their plant a machine that could handle their intense workloads and provide a complete machining cycle.
The benefits derived from using this machinery
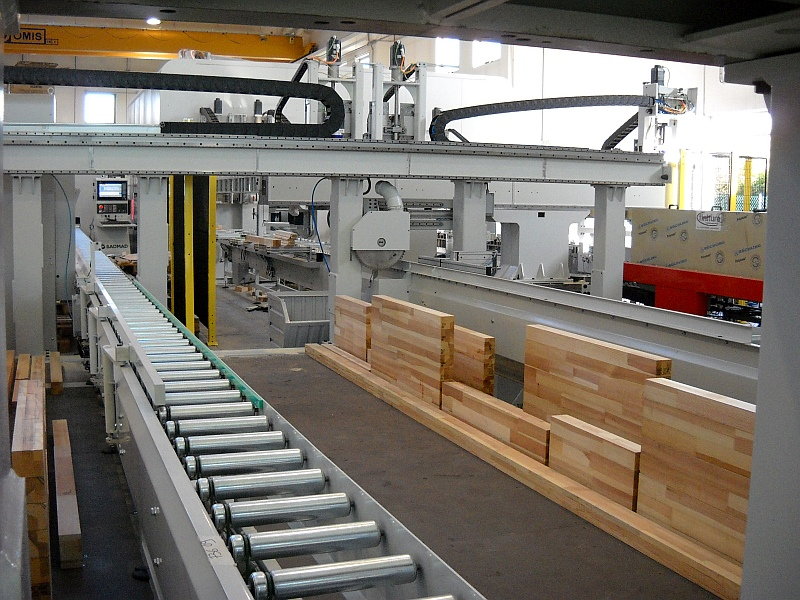
The Woodpecker 60 line offers many advantages:
- unmanned, non-stop processing;
- simple and intuitive machine operation;
- optimized stacking unit;
- unlimited production mixing options also thanks to the possibility of working pieces in the horizontal;
- very small overall size and consumption. It is a very compact line compared to similar solutions available on the market, although it still allows to process and stock pieces up to 6 m long;
- very high production rate thanks to a set of motors dedicated to each processing stage and that can count on a 300-slot tool magazine;
- short tool-changing times also ensure very high performance rates.
We would like to spotlight three innovative features: the intelligent stacking unit, the rack storage unit for finished pieces and the “Genius”, a new generation double-clampdevice that helps reduce loading/unloading time compared to standard devices.
An intelligent stackingunit
The pieces arriving from the sanding machine are picked up by a suction cup manipulator and stacked in the 8-level intelligent stacking unit designed as a stacker.
This unit has considerable storage capacity, i.e. up to 800 pieces, that can be increased according to the client’s needs by adding more 400-piece modules for up to a total of 1,200 pieces. This stacking unit can receive random pieces both manually and from a moulding machine or an optimizer.
Another manipulator fetches the pieces to be machined by the Woodpecker 60 robotized cell, which can work around the clock because the stacking unit can continuously be supplied with pieces.
How does the machine know which pieces to get?
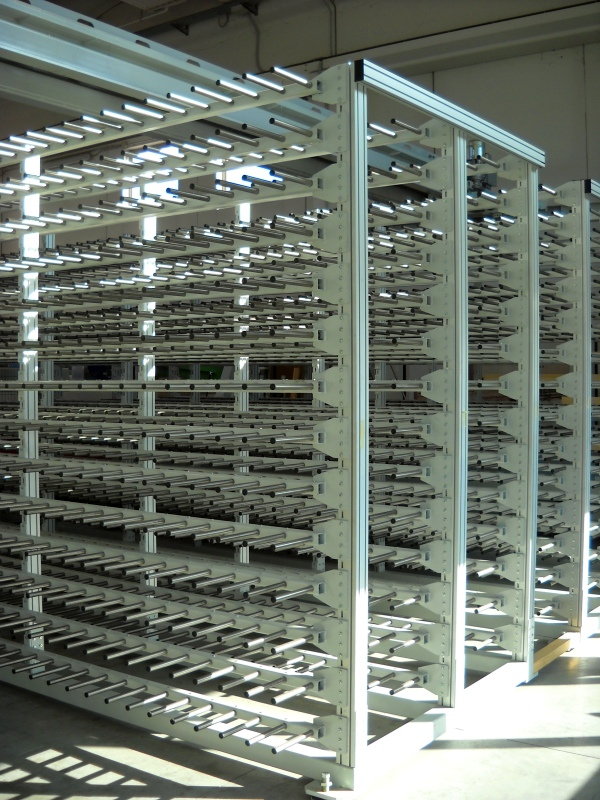
The control software remembers the positioning of each piece and therefore can, for example, pick up in sequence 2 uprights and 2 cross-pieces to make a sash and a frame, or process in series based on how the operator wants to set the work cycle.
The rack storage unit and the Genius double-clamp device
The storage function of this line for the production of wooden doors and windows is completed by a rack storage unit, which consists of 5 14-storey trays on which the finished pieces are automatically placed.
Genius, the double-clamp device that we mentioned before, allows to transfer two machined pieces on the opposite side of the clamps in a very short time so as to clear the machine and allow it to proceed with the next work cycle.
The benefit here comes from the fact that, during such processing, the system fetches another 2 pieces with the second clamp from the intelligent stacking unit and keeps them on stand-by, so that the pieces are ready to be machined in queue, thereby reducing the machine’s overall cycle time.
Ultrasound bath for tool cleaning
More and more frequently, our clients ask us for an advanced tool cleaning system. For this reason, and not only in the Woodpecker 60 but in other smaller machines too, we have added an ultrasound bath placed at the back of the machining centre.
The ultrasound waves propagate through the bath water and remove the dirt and resin deposited on the tools. A specific software even allows to decide which tools need cleaning while the machine is in use.
Final testing and delivery to the client
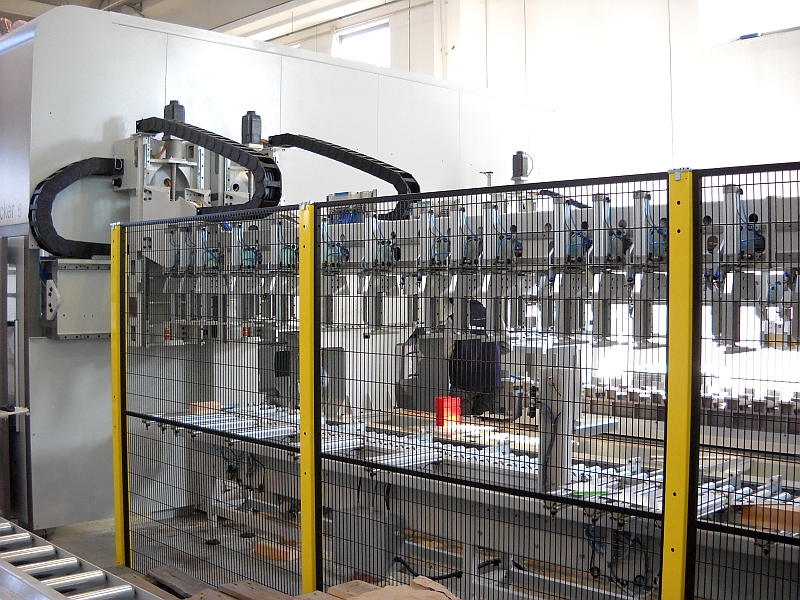
The work required to set up the line started in April 2021 after various meetings, exchange of ideas and revisions.
The final testing was performed at our plant with the client attending. This was an intense week of work during which many processing sessions were carried out so as to instruct the Swiss company’s technicians who in the end gave their favourable assessment of how the machine worked.
At that point, the machine was shipped off to Switzerland. This too was a rather difficult operation, especially from a logistic point of view: indeed, 10 standard and mega trucks were needed, loaded over various work days.
When the last truck left our plant, just days before Christmas, we felt an intense mixture of satisfaction, pride and enthusiasm.